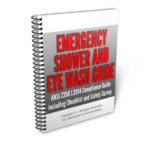
Emergency Eye Flush
Life-Saving Steps to Treat Chemical Eye Exposure
(Don’t Skip These Critical First Minutes)
I’ve seen many eye emergencies. Chemical exposure to eyes how to flush is serious. I’m here to teach you how to flush your eyes properly. This guide helps with emergency eye treatment and preventing injuries.
Being careful with your eyes is crucial. Whether at work or home, knowing how to handle chemical splashes is important. I’ll show you how to react when accidents happen and how to protect your eyes.
Quick action is vital. The right steps in the first few seconds can be lifesaving. Let’s explore this emergency guide and prepare you for any eye issues.
Key Takeaways
- Act fast when chemical exposure occurs
- Flush eyes immediately with clean water
- Know the location of eyewash stations
- Wear proper eye protection in risky areas
- Seek medical help after initial flushing
- Keep emergency eyewash supplies handy
- Learn proper flushing techniques beforehand
Understanding the Risks of Chemical Eye Exposure
Chemical eye exposure is a big risk at work. It’s crucial to know these dangers. We’ll look at the hazards, effects, and what happens when chemicals get in your eyes.
Common Hazardous Chemicals in Everyday Settings
Many products we use can hurt our eyes. Cleaning stuff, pesticides, and some beauty products are risky. In workplaces, acids, alkalis, and solvents are big dangers. Always protect your eyes when using these.
Immediate Effects of Chemical Contact with Eyes
Chemicals touching your eyes can hurt a lot right away. You might feel pain, see red, or have blurry vision. In bad cases, it can cause chemical burns. Knowing how to treat chemical burns is very important.
Chemical Type | Immediate Effects | First Aid Response |
---|---|---|
Acids | Burning sensation, redness | Flush with water for 15-20 minutes |
Alkalis | Severe pain, tissue damage | Flush with water for 30+ minutes |
Solvents | Irritation, tearing | Remove contacts, flush with water |
Long-term Consequences of Untreated Eye Exposure
Not treating chemical eye exposure can cause lasting harm. You might lose vision, get scars, or have eye problems forever. That’s why quick action and the right treatment are key to keeping your eyes safe.
Prevention is the best way. Always wear the right eye protection and follow safety rules. If you get chemicals in your eyes, act fast and get medical help. Your eyes are too important to risk!
Chemical Exposure to Eyes How to Flush: Step-by-Step Guide
When dealing with eye flushing, every second counts. I’ve created a detailed guide to help you through this urgent situation. Here are the key steps for cleaning your eyes properly.
- Find an eyewash station or clean water source right away.
- Remove contact lenses if you have them.
- Tilt your head to the side where your eye is hurt.
- Hold your eye open with your fingers.
- Flush your eye with water for at least 15 minutes.
- Use lukewarm water or saline solution for flushing.
- Blink often while you’re flushing.
- Get medical help after you’ve flushed your eyes.
Remember, different chemicals need different eye wash steps. For acids or alkalis, flush for 30 minutes or more. Always follow safety rules and wear the right gear to avoid eye injuries.
Item | Purpose | Location |
---|---|---|
Portable eyewash bottle | Quick first response | First aid kit |
Sterile saline solution | Gentle eye flushing | Medicine cabinet |
pH test strips | Check eye pH after flushing | Chemical storage area |
Eyeshield | Protect eye post-flushing | First aid station |
By following these steps and being ready, you can handle chemical eye exposures well. Always put safety first and get medical help after you’ve treated your eyes.
Essential First Aid Equipment for Eye Emergencies
Having the right tools for eye safety is key. Being ready for eye emergencies helps prevent serious damage. Let’s look at the must-have first aid items for protecting your eyes.
Emergency Eyewash Station Components
Eye rinse stations are vital for safety. They have a basin, water nozzles, and a lever to start the flow. The water should be warm and flow steadily to clean out debris. Some stations also have alarms to signal emergencies.
Portable Eye Flush Solutions
Portable eye flush kits are great for mobile jobs. They come with sterile saline solution in bottles. I keep them in my car and toolbox for quick use when I’m not near a fixed station.
Personal Protective Equipment (PPE)
PPE is your first defense against eye injuries. You need safety goggles, face shields, and protective eyewear. Choose PPE that’s tough, protects against chemicals, and is comfortable. The best PPE is what you’ll wear all the time.
By having these items and following safety guidelines, you’re making your workplace safer. It’s not just about following rules; it’s about keeping your eyes safe.
Proper Eye Flushing Techniques and Duration
I’ve learned that knowing the right eye-flushing techniques can make a huge difference in emergency eye treatment. When it comes to ocular decontamination procedures, time is of the essence. Let’s dive into the most effective methods for flushing chemicals from your eyes.
First, it’s crucial to start flushing immediately. Don’t wait! Hold your eyelids open and let lukewarm water run over your eye for at least 15 minutes. This might seem long, but it’s necessary to remove all traces of the chemical.
During the flush, look up, down, and side to side to ensure the water reaches all parts of your eye. If you’re helping someone else, gently hold their eyelids open for them. Remember, thorough rinsing is key in these emergency eye treatment situations.
Chemical Type | Flushing Duration | Special Instructions |
---|---|---|
Acid or Alkali | 30 minutes | Use pH-neutral solution if available |
Irritants | 15 minutes | Check for contact lens removal |
Unknown Substance | 20 minutes | Seek immediate medical attention |
After flushing, pat the area dry with a clean towel. Don’t rub your eyes! If you’re still experiencing discomfort or vision changes, seek medical help right away. Remember, proper eye-flushing techniques are your first line of defense in ocular emergencies.
Different Types of Eye Flush Solutions
When dealing with chemical exposure to the eyes, knowing how to flush is key. I’ve looked into different eye flush solutions. This helps you understand their uses in emergency eyewash protocols.
Saline Solutions vs. Plain Water
Saline solutions are better for eye rinsing than plain water. They match the eye’s natural tears, causing less irritation. While plain water is easy to find, it might not be as comfortable but works in emergencies.
Specialized Chemical Neutralizers
For certain chemical exposures, neutralizers are vital. They counteract the pH of harmful substances. Labs often have these solutions ready for quick action in chemical accidents.
pH-balanced Eye Wash Products
pH-balanced products are gentle on the eyes. They flush out contaminants without upsetting the eye’s natural pH. This makes the flushing process less uncomfortable.
Solution Type | Pros | Cons | Best Use |
---|---|---|---|
Saline | Matches tear composition | May not neutralize chemicals | General eye irritation |
Plain Water | Readily available | Can cause slight discomfort | Emergency situations |
Chemical Neutralizers | Targets specific chemicals | Limited to certain exposures | Known chemical contact |
pH-balanced Products | Gentle on eyes | May be more expensive | Prolonged flushing needs |
Choosing the right solution is crucial for effective emergency eye wash protocols. It’s important to have the right options in eye rinse stations. This ensures quick and proper treatment for different chemical exposures to the eyes.
When to Seek Professional Medical Help
Quick action is key in treating chemical burns. Flushing your eyes is the first step. But knowing when to get professional help is crucial for your vision.
Severe pain, blurred vision, or trouble opening your eyes after flushing are warning signs. These symptoms mean serious damage and need emergency eye treatment. Vision protection guidelines stress the importance of quick care to avoid long-term problems.
Here’s a quick guide for when to seek help:
Symptom | Action Required |
---|---|
Persistent pain after flushing | Seek immediate medical attention |
Blurred or decreased vision | Go to the emergency room |
Difficulty opening eyes | Call for emergency assistance |
Visible eye damage | Urgent ophthalmologist consultation |
Trust your instincts. If something feels wrong, even after following first aid steps, it’s safer to seek help. Your eyes are very important. Quick professional care can help save your sight.
Workplace Safety Protocols for Eye Protection
Keeping your eyes safe at work is very important. It’s not just about wearing goggles. It’s about making a whole system to protect the eyes.
OSHA Requirements for Eye Wash Stations
OSHA has strict rules for eye wash stations. They must be easy to get to and ready to use at all times. They need to have 15 minutes of clean, warm water flowing. Keeping them in good shape is very important.
Employee Training Guidelines
Training is key to preventing eye injuries. Workers must know how to use protective gear and eye wash stations correctly. Hands-on practice is best. It helps them remember what to do in emergencies.
Emergency Response Procedures
Quick action is very important when eye injuries happen. Every workplace needs clear eye wash protocols. These should include:
- Steps to immediately flush eyes
- How to call for medical help
- Proper documentation of incidents
To make sure eyes are safe at work, I’ve made a table of important things:
Safety Element | Description | Frequency |
---|---|---|
Eye Wash Station Checks | Inspect for cleanliness and function | Weekly |
Safety Gear Inspections | Check goggles and face shields for damage | Daily |
Employee Training | Review eye safety procedures | Quarterly |
Emergency Drills | Practice eye injury response | Bi-annually |
By following these steps, workplaces can greatly lower eye injury risks. They can also make sure they respond quickly and well when injuries happen.
Prevention Strategies and Best Practices
Keeping our work area safe is key. I’ve learned that eye safety measures can really help. By following safety guidelines, we make our workplace safer for everyone.
Let’s look at some important eye protection strategies:
- Wear the right safety goggles or face shields
- Put eyewash stations where they’re easy to find
- Have regular safety training
- Handle dangerous chemicals carefully
- Keep chemicals labeled and stored right
Handling chemicals safely is very important. I make sure chemicals are in sealed containers. I also use funnels or pumps to avoid spills when moving them.
Protecting our eyes is more than just goggles. Using splash guards and good ventilation also helps a lot.
Here’s a list of safety gear we should use:
Equipment | Usage | Maintenance |
---|---|---|
Safety Goggles | Wear during all chemical handling | Clean daily, replace if scratched |
Face Shields | Use for high-risk tasks | Inspect before each use |
Eyewash Stations | Know locations and how to use | Test weekly, keep the area clear |
By using these strategies, we can make our workplace safer. Remember, it’s always better to prevent eye injuries than to treat them.
Recovery and Follow-up Care After Chemical Exposure
After getting chemicals in your eyes, it’s important to take care of them. I’ll show you how to help your eyes heal and avoid lasting damage.
Monitoring Eye Health Post-exposure
Watch your eyes closely after a chemical burn. Look for signs like redness, pain, or blurry vision. If these signs don’t go away or get worse, see a doctor right away. Going to the eye doctor regularly is key to seeing how well you’re healing.
Documentation and Incident Reporting
It’s important to write down all the details about what happened. This includes:
- Date and time of exposure
- Chemical involved
- Emergency eye treatment received
- Symptoms experienced
Tell your workplace safety officer or the right people about the incident. This helps keep everyone safe and makes sure you get the right care.
Long-term Treatment Options
Some chemical burns need ongoing treatment. Your doctor might suggest:
Treatment | Purpose |
---|---|
Antibiotic eye drops | Prevent infection |
Lubricating eye drops | Relieve dryness and discomfort |
Corticosteroid eye drops | Reduce inflammation |
Surgical procedures | Repair severe damage |
Quick action and professional help are crucial. They help reduce long-term effects and help your eyes fully recover from chemical exposure.
Specialized Situations and Chemical-Specific Protocols
When dealing with chemical eye exposure, flushing methods vary. Each chemical needs its approach. Let’s look at some special cases and their emergency eye wash plans.
For alkali burns, flushing for at least 30 minutes is key. These chemicals can go deep into the eye. Acid burns, on the other hand, need 15-20 minutes of rinsing.
With organic solvents like gasoline, water alone might spread the chemical. In such cases, special eye wash solutions work better. They help break down the chemical, making it easier to remove.
Chemical Type | Flushing Duration | Recommended Solution |
---|---|---|
Alkalis | 30+ minutes | Water or saline |
Acids | 15-20 minutes | Water or saline |
Organic Solvents | 15-20 minutes | Specialized emulsifying solution |
For dry chemicals, brush off the substance before flushing. This stops the chemical from reacting with water. These special steps are vital to reduce damage and treat the eye effectively.
Conclusion – Chemical Exposure to Eyes How to Flush
I’ve talked a lot about chemical exposure to the eyes and how to flush them. Quick action is very important for eye injuries. Knowing how to flush your eyes right can save your vision.
Preventing eye injuries is key at work and at home. Follow safety guidelines to avoid chemical accidents. Always wear safety goggles and keep eyewash stations ready.
If you get chemicals in your eyes, don’t worry. Flush them with clean water or eye wash solution for 15 minutes. Then, get medical help right away. Your eyes are very important, and these steps can protect your sight for a long time.
FAQ – Chemical Exposure to Eyes How to Flush
How long should I flush my eyes after chemical exposure?
Always flush your eyes for 15-20 minutes. Sometimes, you might need to do it for up to 30 minutes. It’s safer to flush longer than you think.
Can I use regular tap water to flush my eyes in an emergency?
Yes, tap water is okay if you have no other choice. But, a sterile saline solution is better if you can get it.
What should I do if I don’t have access to an eyewash station?
Use any clean water you can find. This could be a sink, shower, or even a water bottle. Start flushing right away and do it for 15 minutes.
Should I remove my contact lenses before flushing my eyes?
Yes, take out your contact lenses quickly. They can trap chemicals and make things worse. If they don’t come out, keep flushing and let a doctor remove them later.
Is it safe to use eye drops after chemical exposure?
No, don’t use regular eye drops. They’re not made for this and might interfere with treatment. Flush with water or saline and see a doctor.
How can I tell if my eye injury requires professional medical attention?
Always be safe. See a doctor if you have pain, blurred vision, swelling, or if the chemical is powerful. If unsure, it’s best to get checked.
What’s the proper technique for flushing eyes?
Tilt your head so the affected eye is lower. Hold your eyelids open with your fingers. Let the water run from the inner corner of your eye outward.
Are there any chemicals that shouldn’t be flushed with water?
Some chemicals can react badly with water. But, in an emergency, flushing with water is usually the best first step. Tell a doctor about the chemical you were exposed to.
How often should workplace eyewash stations be inspected?
Eyewash stations should be checked weekly. Make sure they work, are clean, and the solution is fresh.
What should be included in a workplace eye safety program?
A good eye safety program should include PPE, hazard identification, and emergency response training. It should also cover how to use eyewash stations and incident reporting.
ANSI Z358.1 2014 Compliance | It’s Important ! | Emergency Shower and Eye Wash